A
Good Tool for Custom Pipes |
Whenever you need to route a pipe around something, a
good method is to get some thick household electrical
wire, or fence wire, or old brake line (it really
doesn't matter as long as it can hold its shape).
You take this and bend it how you would like your pipes
to run. Take this to the store and say "Can you
make me a pipe that is 'X' diameter and bent like this"
(hold up wire)? Make their lives easier and don't
make too tight of radiuses for larger pipes. |
Turbo Oil & Water Lines |
Lets start with the oil and water lines for the turbo. Mixing and
matching Starion and DSM banjo fittings, I
have got a pretty nice setup. I cut some of the
hard lines in half and used 3/8" to extend them.
For the Oil inlet line I bought a SS line from RRE
and will be doing a modification that moves the source
from the banjo bolt at the back of the head to the
freshly filtered, higher pressured source at the oil
filter bracket as you can read
here. |
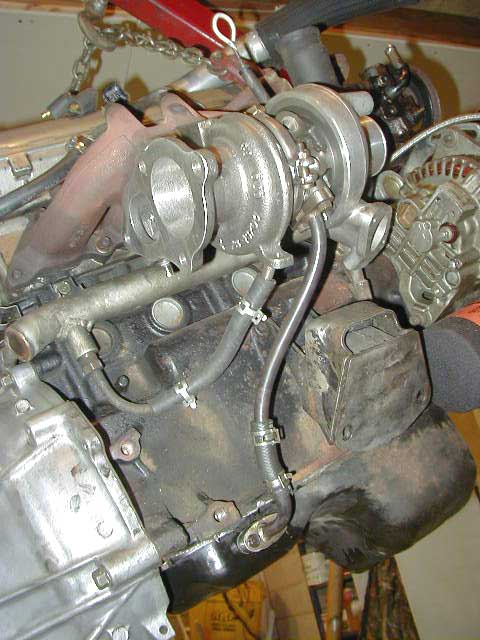 |
I had to get even more creative with the oil drain.
It will see very little pressure, but it will be mounted
directly to the hot center cartridge and will have hot
oil flowing through it. Unlike the water lines, if
this oil line blows out the effects would be fiery and
most likely the end of the motor and turbo. So what
dad and I decided to do was to make new flanges and weld
custom bent pipes from the turbo to the oil pan.
There is a small section of rubber hose closer to the
oil pan. Hopefully this will not get so hot that
it fails. "But isn't custom bending oil lines
hard, and won't they kink?" No! What we did
was very neat. Since it is winter, we just threw
the pipe in the wood stove for about 5 minutes. It
came out red hot and we easily could bend it with the
vice, and plyers. I let it touch my skin once.
OMFG. It didn't burn my skin... it turned it
straight to yellow ash. So watch yourself.
(Also works well with bon fires.) Just be sure to
bend the pipe so that it clears the motor mounts and
crossmember. |
Engine Water Pipes |
These are the pipes that connect the radiator to the
motor. There is an 'In' and 'out' of the block.
The 'in' comes from the bottom outlet on the radiator
along with the turbo return and heater/TB return.
The 'out' line comes from the water neck that comes off
of the thermostat at the back of the head (what a stupid
spot to put it). So here is one way to do it. |
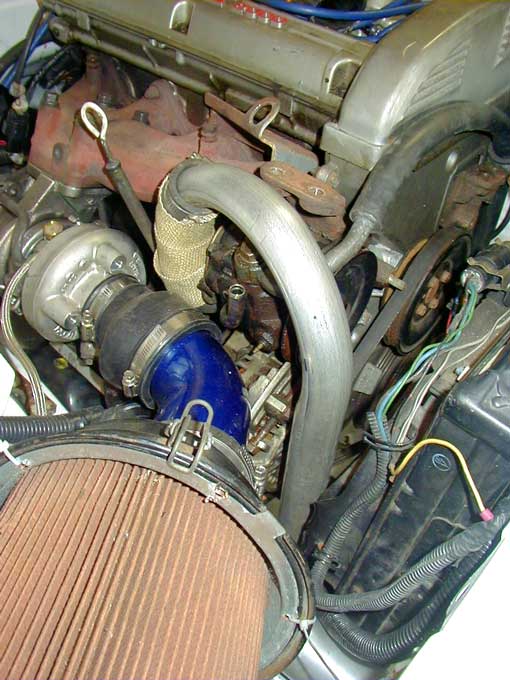 |
Starting with the 'in' side that flows into the water
pump there is a large pipe that runs under the exhaust
manifold and around to the heater core on the back of
the block. This is thing aluminized steel.
What you should do is cut the end of the big section off
(see the photo above). I took what I cut off and
weld it to the pipe up near the alternator. Try
not to do this. You would be better off to weld a
piece of pipe on that is long enough to clear the
alternator and all that. I on the other hand will
have a rubber hose running right in between my
alternator and exhaust manifold. I do, however,
have it heat wrapped. From here I have gotten a
pipe bent to go to the radiator. It twists up over
top of the power steering pump and then down between the
fans and the alternator. The shop that I had the
pipe bent at only had 1 1/2" pipe. I really needed
1 1/4". luckily they crush bent it. This
narrowed the pipe down enough that my rubber water hoses
would fit on. |
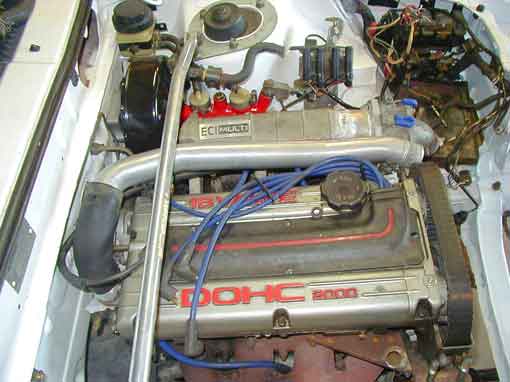 |
Coming from the termostat I used one of the pipes off of
the intercooler since I won't be needing it anymore.
To go to the radiator all you need is the straightest
section of IC hose from either the Starion or the DSM.
Don't cut it too short!!! I had to go to the
junkyard to find one because I cut 4 of them too
short (Doh!). There is one that is a perfect fit.
Don't ask me which car it was off of though. |
|
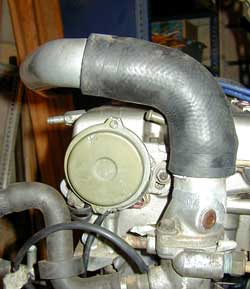 |
Coming down over the top of the motor around back I used
one of the IC elbows off of one of the cars, then had
the other (short) intercooler pipe welded to my hacked
up water neck. To plug up the A/C temp sensor
hole, I used the plug that came out of where my new SS
oil line went. Reduce/Reuse/Recycle! This
setup reused a lot of parts and kept the valve cover
accessible. It also clears the hood and strut
tower brace. Man does it look pretty too. |
|
Heater Hoses |
To keep even a little bit of comfort during the winter,
I have to keep my heater. For these hoses, I just
reused some heater hoses off of either the DSM or
Starion. Forget which one came from which, but mix
and match and you can find some. If you can't,
however, you will need to find some hose that can hold
pressure and take the heat. You might need to get
creative (and long) with it to get it to bend right.
If you cannot find anything that can work, take your
bent wire to the auto parts store and see what might
work. |
Intake |
As you can see from one of the above photos, all I used
was a 3" elbow. I actually just cut up an
aluminum, powder coated cold air intake off of an IS300.
I then used some plumbing supplies to hook everything
up. The turbo inlet coupler will be replaced by a
silicone reducer at some point due to the heat it sees
from the compressor housing. |
Intercooler Pipes |
I got crafty with these hoses as well. For the hot
side, I found an old aluminum pipe off of a vacuum
cleaner in my woods. 2" mandrel bent aluminum.
If you want some 2" mandrel bent aluminum, I hear Justin
at www.up-speed.com
can get bends for $25 a pop! For the cold side I
used another thing I found in the woods. 2.5"
mandrel bent aluminum pipe. I think my brother got
it off of a Volvo intercooled car or truck. Either
way it routes through a rust hole that formed next to my
radiator and below my battery. This allows me to
get away with using the stock battery location, but with
a narrower battery. Why'd I used 2 different sizes?
Because that's all I could find in the woods! But
I did think about it some. The compressor outlet
is only 1 7/8". The air is flowing very fast out
of the turbo. Why slow it down by going big right
away? I keep it moving fast till it gets to the
intercooler where it spreads out and slows down (and
hopefully cools down). From here it is already
moving slow. Why stuff it into a small pipe again?
2.5" is the largest diameter pipe I could fit between
the battery and the radiator. This goes up to a
bend that goes into the throttle body. I heat
wrapped the pipe after the intercooler so that it
doesn't soak up any heat from the radiator or engine
bay.
To attach the 2" and 2.5" pipes to the intercooler,
we made some modifications. My uncle, the master
that he is welded a beaded end that I cut off the
aforementioned Volvo IC pipe and a beaded end cut from
the 2" Vacuum cleaner pipe to the intercooler end tanks.
We cut off the stock IC inlets and capped them off with
some bitchin' aluminum diamond plate!
We moved the intercooler up to the top of the
radiator. Calvin gets full credit for this idea.
This was really done to simplify the routing and reduce
the bends in the intercooler pipes. This too has
some added benefits. The intercooler is now less
likely to eat rocks and curbs and it doesn't pick up the
warm air that resides just above the pavement on hot
sunny days. I've ran the car very hard and have
never felt the intercooler get heat soaked.
The intercooler is supported in its new location
mainly by the silicone elbows with zip-ties as added
support. It is pretty easy to steal (2 zip ties
and 2 hose clamps). So I will be adding some
ducting. This will make the intercooler herder to
steal. Plus it will keep the air heated from the
oil cooler out of the intercooler. It will also
scoop air from below and route it up to the radiator. |
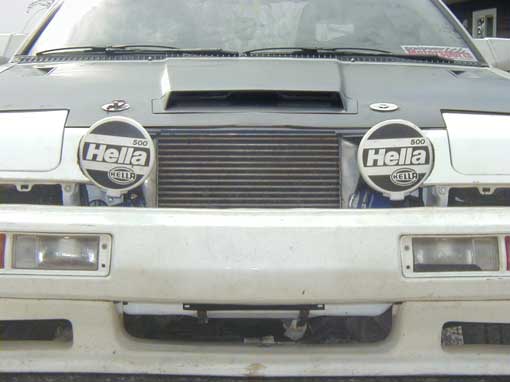 |
Downpipe |
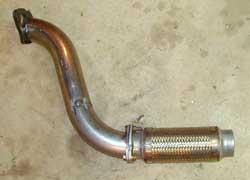 |
The exhaust on this car has to be pretty custom (what
isnt). I ordered a flange from RRE and some found
some 3" mandrel bends locally. It's pretty
straight forward. This photo shows the basic bends
of the exhaust. |
We found some pipes in my uncle's shed which we used for
the wastegate tube sections. We didn't measure
very well though. The wastegate actually runs into
the firewall a little so we had to
bang it out(3.2MB
video). The oxygen sensor bung is actually the
bung off of the Starion's primary cat. The DSM O2
sensor screws right into it. |
 |
Power Steering Lines |
Don't think too hard with this one. You don't need
-AN fittings and all that fancy stuff. You can use
the DSM's high pressure line and low (100psi) pressure
oil compatible hose. The DSM power steering line
does not work with the Starion gearbox. At first I
tried to use D50 power steering lines, but they also
have different fittings (o-rings). The Starion
gearbox uses simple flared fittings, as does the rubber
section of the DSM high pressure line.
|
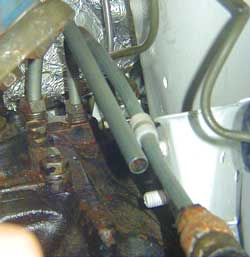 |
I simply removed the flare nuts off of the old
Starion P/S lines and off of the DSM high pressure line.
I then bought some 3/8" hardline used for either a fuel
line or brake line. Every parts store has a rack
of these. You don't need but maybe 12". I
cut one end off of the hardline to remove both flare
fittings. I slid the DSM flare on one side and the
Starion flare on the other. Then I double flared
the end I had cut. To put it on the car you need
to bend the hardline about 90 degrees in a graceful
bend. No need for a tight radius. The
Starion flare goes right into the Starion gearbox and
the DSM flare goes into the DSM high pressure line.
For the low pressure line, you need ??" hardline.
cut one end off. Remove the fitting and slide on
the Starion fitting. You can then slide your low
pressure oil hose over the cut end. Hose clamp
that bastard and route your low pressure line.
Don't forget to tie it into the power steering cooler
that runs across the front of the bumper. The best
way to route the high pressure line, is right in front
of the timing cover. You can use any power
steering reservoir you want. I used the DSM one
due to the locations of the inlet and outlets. It
also bolted into the stock location without
modification. I used lines from either the Starion
or DSM to connect it to the power steering pump. |
|